生產效能革命:能源管理系統(tǒng)如何重塑制造業(yè)競爭力
在全球能源轉型和"雙碳"目標的大背景下,制造業(yè)正面臨前所未有的能源管理挑戰(zhàn)。據統(tǒng)計,工業(yè)領域占我國總能耗的65%以上,其中制造業(yè)能耗占比超過50%。隨著能源價格波動加劇和環(huán)保要求日益嚴格,傳統(tǒng)的粗放式能源管理模式已難以適應發(fā)展需求。某汽車集團能源審計數據顯示,其生產基地存在高達30%的潛在節(jié)能空間,這反映出制造業(yè)在能源管理方面的巨大改進潛力。
現代能源管理系統(tǒng)通過對生產設備的精細化管理,實現了能效的全面提升。在某大型裝備制造企業(yè)的數字化車間,系統(tǒng)接入了超過2000個能源監(jiān)測點,構建了完整的設備能效畫像。通過實時數據采集和分析,企業(yè)發(fā)現了三大能效提升機會:
設備空載優(yōu)化:識別出28臺存在空載耗能問題的設備,通過智能啟??刂?,年節(jié)約電能消耗150萬度。
負載匹配調整:對12臺長期處于低效區(qū)的加工中心進行工藝參數優(yōu)化,設備能效提升22%。
預防性維護:基于能耗特征變化預測設備故障,維修響應時間縮短60%,意外停機減少45%。
能源管理系統(tǒng)與生產過程的深度融合,帶來了工藝控制的革命性進步。以某化工企業(yè)為例,系統(tǒng)實現了:
- 關鍵參數精準控制:反應釜溫度控制精度從±2℃提升到±0.3℃,催化劑使用效率提高18%。
- 能源介質協(xié)同優(yōu)化:建立蒸汽、電力、循環(huán)水的智能調配模型,整體能效提升15%。
- 工藝路線創(chuàng)新:通過能源流分析,優(yōu)化了蒸餾塔操作參數,單套裝置年節(jié)約蒸汽費用800萬元。
能源管理系統(tǒng)構建了多維度的安全防護體系:
- 電氣安全監(jiān)控:某化工廠通過實時監(jiān)測電纜接頭溫度,成功預警了5起潛在電氣火災。
- 應急能源保障:關鍵設備雙路供電的智能切換系統(tǒng),保障了99.99%的供電可靠性。
- 安全閾值管理:設置200多個用能安全參數閾值,實現超限自動保護。
能源大數據正在改變制造企業(yè)的決策方式:
- 設備更新決策:某企業(yè)依據能效數據,優(yōu)先改造了能效最低的20%設備,投資回報期縮短40%。
- 產品結構調整:通過產品能耗分析,淘汰了3個高耗能低利潤產品,整體利潤率提升6%。
- 產能規(guī)劃優(yōu)化:新建生產線設計充分考慮了能源管理需求,單位產能能耗降低25%。
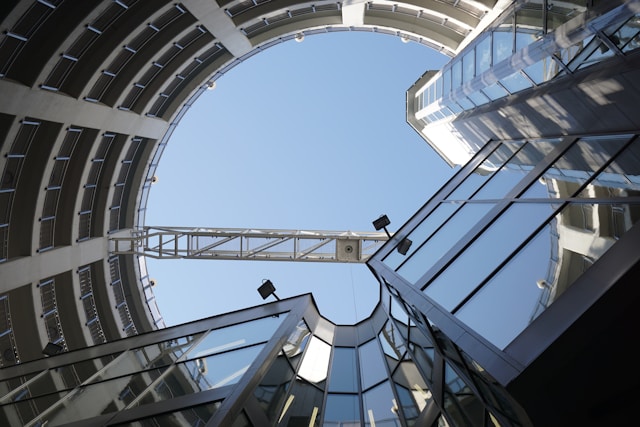
能源管理系統(tǒng)正在引發(fā)制造業(yè)生產模式的深刻變革。從單一設備到整個生產系統(tǒng),從操作層到決策層,能源管理能力的提升帶來了全方位的效能改進。在智能制造和綠色發(fā)展的雙重驅動下,那些率先完成能源管理數字化轉型的企業(yè),已經建立起顯著的競爭優(yōu)勢。未來,隨著技術的持續(xù)進步,能源管理系統(tǒng)必將成為制造業(yè)高質量發(fā)展的核心支撐,為企業(yè)創(chuàng)造更大的價值空間。